نفت و گاز
رادیوگرافی
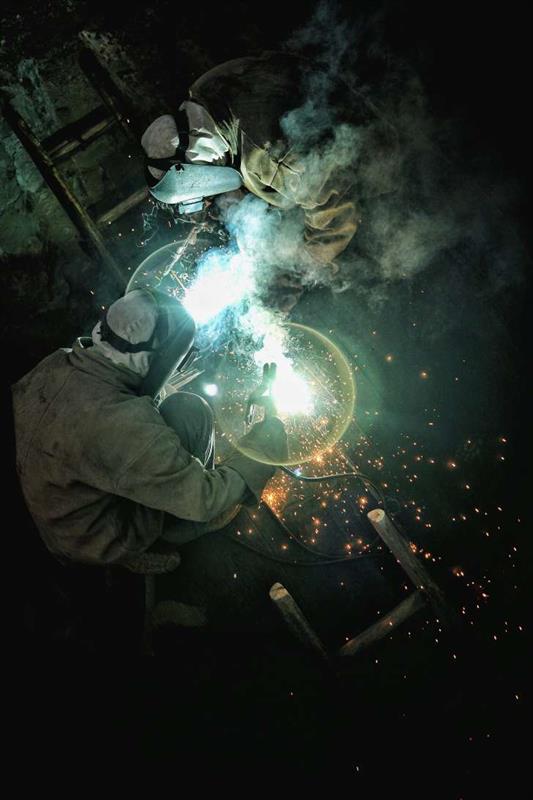
مقدمه
روش های مختلفی برای ساخت قطعات مانند ریخته گری ، شکل دهی ، جوشکاری و متالورژی پودر وجود دارند که هر کدام از این روش های مزایای مربوط به خود را داشته و با درنظرگیری کابرد قطعه موردنظر در حین سرویس روش مناسب برای ساخت آن بایست انتخاب گردد. بدیهی است قطعه ای که توسط هرکدام از این روش ها تولید می شود عیوب مربوط به آن روش ساخت را به همراه دارد. به عنوان مثال قطعات تولید شده توسط روش ریخته گری دارای عیوبی مانند انقباض ناشی از سرمایش ، ترک های گرم ، جدایش متالورژیکی ، تخلخل و اسفنجی بودن هستند. همچنین شکل دهی عیوبی مانند ورقه ای شدن ، روی هم افتادگی و پارگی مرکزی می باشد. جوشکاری که یکی از مهمترین و پرکاربردترین روش های تولید و سر هم کردن قطعات و ابزارالات است نیز دارای عیوب متعددی مانند سوختگی کناره جوش ، عدم نفوذ ، ذوب ناقص یا عدم ذوب و ترک های جوشکاری می باشد. در صنعت برای بررسی و یافتن عیوب در قطعات تولید شده روش های مخرب و غیرمخربی وجود دارد. منظور از روش های غیرمخرب روش هایی است که بدون اسیب زدن به قطعه موردنظر آن را عیب یابی می کند. از جمله این روش ها آزمون مایع نافذ ، آزمون ذرات مغناطیسی ، آزمون اولتراسونیک و آزمون پرتونگاری یا رادیوگرافی می باشد. در این گزارش ابتدا یک سری از عیوب ایجاد شده در جوشکاری و فیلم های رادیوگرافی آن جهت آشنایی ارائه می شود و سپس نحوه عیب یابی این عیوب توسط روش رادیوگرافی بیان می شود.
بخش اول: برخی از عیوب جوشکاری
یکی از عیوب معمول در جوشکاری روی هم افتادگی یا انباشتگی جوش در کناره ها می باشد. روی هم افتادگی درحقیقت نقصي در کناره يا ريشه جوش است که به علت جاري شدن فلز جوش بر روي سطح فلز پايه ايجاد مي شود بدون اينکه ذوب و جوش خوردن با آن انجام شود (شکل 1 شکل 2). دلیل آن سرعت حرکت کمتر از حالت نرمال يا طبيعي، زاويه نادرست الکترود، استفاده از الکترود با قطر بالا و آمپراژ خيلي کم در فرآیند جوشکاری میباشد.
یکی دیگر از عیب های بسیار معمول در فرآیند جوشکاری سوختگي يا بريدگي کناره جوش می باشد. سوختگی کنار جوش درحقیقت يك شيار بي قاعده روي فلز پايه در اطراف خط جوش و افتادگي كناره جوش مي باشد. علت بوجود آمدن آن جريان جوشكاري بيش از حد زياد، سرعت جوشكاري خيلي زياد، زاويه غیر صحیح الكترود، موجي دهي بیش از حد الكترود و استفاده از الكترودهای خيلي قطور می باشد.
آخال هاي سرباره از دیگر عیوب ایجاد شده در جوشکاری هستند. آخال سرباره عبارت است از ناخالصي هاي غير فلزي گرفتار شده در حوضچه جوش كه معمولاً منشا آن از پوشش الكترود است. علت بوجود آمدن ناخالصي هاي سرباره اي، عدم تميز كاري كافي گل جوش بين پاس هاي متوالی، آلوده بودن سطح اتصال آماده شده، جوشكاري برروي يك سطح با انحناء نامنظم، نامناسب بودن سرعت جوشكاري و طول قوس خيلي زياد می باشد.
تقعر در جوش یکی دیگر از عیوب فرآیند جوشکاری می باشد. فرورفتگي که سطحی بوده و عمق آن از قطر دهانه اش کمتر است را در ريشه جوشهاي لب به لب تقعر در ريشه مي نامند. واژه هاي ديگري نيز به اين عيب اختصاص داده شده است که عبارتند از مکش به عقب و تخليه ريشه جوش . از دلایل ایجاد آن می تواند سطح ریشه خيلي بزرگ، انرژی قوس ناکافی و دميدن بيش از حد گاز در پشت جوش هنگام جوشکاري به روش TIG می باشد.
یکی از مهمترین عیوب جوش عدم ذوب یا ذوب ناقص می باشد. به عدم الحاق ماده در يك جوش عدم ذوب مي گويند .عدم الحاق در يك جوش ممكن است به سه صورت به وجود آید:
- بين فلز جوش و فلز پايه
- بين فلز پايه و فلز پايه
- بين فلز جوش و فلز جوش.
علت بوجود آمدن عدم ذوب می تواند سطوح وقطعات آلوده، آمپر خیلی پایین دستگاه جوشكاري و همچنین آمپر خيلي بالای دستگاه باشد بطوريكه سرعت انتقال الكترود زياد بوده و يك عدم ذوب در لايه هاي فلز بوجود آید.
از دیگر عیوب تخلخل می باشد. درحقیقت تخلخل حفره ای است كه قطر آن زير 5/1 میلیمتر بوده و در اثر جذب گاز در هنگام انجماد فلز ذوب شده بوجودآيد. علت بوجود آمدن آن رطوبت بيش از حد فلاكس، رطوبت بيش از حد در هنگام آماده سازي مقطع جوش، آلوده بودن لبه ها به پوسته، لايه اكسيد و غيره، بكارگيري جريان جوشكاري كم و يا زياد، طول قوس بيش از حد زياد، آسيب ديدگي روپوش الكترود، تكنيك غلط موج دهي الكترود و دور شدن گاز محافظ از اطراف جوش مثلاً در اثر وزش باد در سايت می باشد. تخلخل می تواند فرم های مختلفی داشته باشد که به شرح ذیل است:
Blowhole :حفره اي كه معمولاً قطري بيشتر از 1.5mm دارد .
Worm Hole يا Piping :حفره دراز شده يا حفرهاي با مقطع لوله اي
Hollow bead :حفره اي دراز شده در ريشه جوش
Herring bone porosity :حفره هايي كه به صورت بغل به بغل و به شكل استخوان دم ماهي هستند .
یکی دیگر از عیوب مهم جوش عدم نفوذ می باشد. عدم نفوذ یک اتصال نفوذ نکرده در ریشه جوش می باشد. علت بوجود آمدن آن دهانه خیلی عمیق جوش، فاصله خیلی کم بين دو قطعه، طول خیلی زیاد قوس، انتخاب پلاريته اشتباه، الكترود خيلي قطور است و زاويه غلط الكترود می باشد.
از دیگر عیوب جوش ترک می باشد. عدم پيوستگي خطي ناشي از شكست را ترك گويند .
تركهاي جوشكاري عبارتند از:
- تركهاي ناشي از انجماد (Solidification crack)
- تركهاي ناشي از حضور هيدروژن(Hydrogen Induced Cracking)
- ترك يا پارگي سرتاسري (Lamellar tearing)
- ترك هاي ناشي از گرم كردن مجدد (Reheat cracks)
از دیگر عیوب ناخالصي تنگستن می باشد که در هنگام جوشکاري به روش TIG از الکترود تنگستن بوجود مي آيد.
یکی دیگر از عیوب جوشکاری سوختگي داخلي می باشد. فرو رفتن موضعي حوضچه ذوب شده ناشي از نفوذ بيش از حد که سبب بوجود آمدن سوراخي در خط جوش مي شود را سوختگي داخلي ميگويند. اصولا سوختگي داخلي بيشتر با ريشه هاي جوش هاي لب به لب عجين مي باشد. دلایل آن عبارت است از:
• آمپر بيش از حد در هنگام جوشکاري پاس ريشه در جوش هاي لب به لب
• بيش از حد سنگ زدن ريشه جوش که اين موضوع ممکن است سبب سوختگي داخلي پاس دوم شود.
حفره انتهائي یکی دیگر از عیوب معمول در جوشکاری می-باشد. حفره ناشي از انقباض در انتهاي خط جوش همانجائي که منبع حرارت ( الکترود ) از سطح جوش برداشته شده است را حفره انتهائي مي گويند. حفره انتهائي در حقيقت يک نوع عيب انقباضي مي باشد و نبايستي آن را با سوختگي داخلي و يا حفره گازي اشتباه کرد. علت بوجود آمدن این عیب واکنشهاي اکسيداسيون و تغيير حجم ناشي از تبديل مذاب به جامد می باشد.
پاشش يا ترشح نیز یکی از عیوب دیگر فرآیند جوشکاری است. قطرات کوچک از مذاب که به طور ناخواسته از منطقه قوس به اطراف پراکنده مي شوند و ممکن است سبب ذوب يا عدم ذوب فلز پايه شوند را ترشح يا پاشش مي گويند. علت بوجود آمدن پاشش يا ترشح انرژي بيش از حد قوس، طول بيش از حد قوس، استفاده از الکترود مرطوب و وزش قوس است. وزش قوس تغيير مسير قوس در اثر بوجود آمدن ميدان الکترومغناطيس در اطراف قوس در هنگام جوشکاري مي باشد.
بخش دوم: اصول ابتدایی رادیوگرافی صنعتی
اصول رادیوگرافی بر این اساس است که بر اثر تابش پرتو رادیواکتیو به یک قطعه و تفاوت ضریب جذب آن پرتو رادیواکتیو در اجسام مختلف تصویری از قطعه مورد نظر بر روی فیلم رادیوگرافی تشکیل می شود. قطعه مورد نظر می تواند یک آلیاژ ریخته گری شده، یک قطعه فورج شده و یا یک فلز جوش باشد. رادیوگرافی یکی از اساسی ترین و مهم ترین روش برای تشخیص عیوب در اتصالات ایجاد شده در فرآیند جوشکاری می باشد. بازرسی غیر مخرب فلز جوش توسط روش رادیوگرافی به دلایل زیادی نسبت به دیگر روش های بازرسی غیرمخرب ارجح می باشد. نحوه کار بدین صورت است که یک فیلم رادیوگرافی در مجاورت فلز جوش قرار داده شده و از طرف مقابل پرتو رادیواکتیو بر روی فلز جوش تابانده می شود. پرتو رادیواکتیو بر مولکول AgBr واقع در فیلم تاثیرگذاشته و به نحوی آن را یونیزه می کند. به عبارت دیگر پس از پرتودهی مولکول های AgBr موجود در فیلم دچار شکست شده ویون های نقره و بریلیوم به وجود می آیند. پس از پایان پرتودهی فیلم های پرتو دهی شده باید ظاهر شوند. این کار به واسطه فرآیند ظهور و ثبوت انجام می شود. ابتدا فیلم در محلول ظاهر کننده به مدت زمان معینی قرار داده شده و سپس به مدت زمان معین در محلول تثبیت کننده قرار داده می شود. در ظاهر سازی فیلم رادیوگرافی در فرآیند ظهور و ثبوت تصویر یون های نقره به اتم های نقره تبدیل شده که با رنگ سیاه در فیلم رادیوگرافی مشخص می شوند. از آنجاییکه ضریب جذب پرتو در فلز جوش بیش از هوا است فلز جوش مانع از رسیدن پرتو به فیلم شده و تصویر فلز جوش بر روی فیلم رادیوگرافی به واسطه کمتر یونیزه شده مولکول های AgBr نقش می بندد. در صورت وجود هرگونه عیب در فلز جوش تصویر آن به صورت متفاوت نسبت به فلز جوش بر روی فیلم رادیوگرافی نقش میبندد.
عملیات رادیوگرافی به صورت تک دیواره و دو دیواره انجام می شود. در حالت تک دیواره یک لایه فلز جوش بین چشمه و فیلم می باشد درحالیکه در حالت دو دیواره دو لایه فلز جوش بین چشمه و فیلم می باشد. حالت های رادیوگرافی تک دیواره و دو دیواره به ترتیب در شکل های 26 و 27 نشان داده شده است.
عوامل تاثیرگذار بر کیفیت تصویر عبارتند از:
موارد هندسی: فواصل بین چشمه رادیواکتیو-فیلم و قطعه-فیلم. اگر شرایط هندسی به صورت صحیح رعایت نشود عدم وضوح هندسی در فیلم ایجاد می شود. برای کاهش عدم وضوح هندسی باید سایز چشمه کوچک باشد، فاصله چشمه تا جوش بیشترین حالت باشد و فیلم تا حد امکان به قطعه چسبیده باشد.
ویژگی های فیلم: دانه بندی و تضاد تصویر. هرچه سایز دانه فیلم اولیه بالاتر باشد حساسیت و تضاد تصویر تشکیل شده کمتر می شود درحالیکه زمان انجام رادیوگرافی کاهش می یابد. به صورت برعکس هرچه سایز دانه فیلم اولیه بالاتر باشد حساسیت و تضاد تصویر تشکیل شده بیشتر شده و زمان لازم برای پرتودهی افزایش می یابد. به عبارت دیگر زمان بیشتری برای یونزاسیون مولکلول های AgBr لازم است. سایز دانه اولیه فیلم به پارامتر فاکتور فیلم بیان می شود.
کیفیت تشعشع: ولتاژ دستگاه های اشعه ایکس و ناپایداری پرتو گاما از طریق پرتودهی یک رادیوایزوتوپ. هرچقدر ولتاژ دستگاه اشعه ایکس بیشتر باشد پرتویی با فرکانس بالاتر ایجاد می کند. همچنین هرچقدر رادیوایزوتوپ ساطع کننده اشعه گاما ناپایدارتر باشد پرتویی با فرکانس بالاتر ایجاد می کند. لازم به ذکر است که دستگاه اشعه ایکس با برق کار می کند درحالیکه رادیوایزوتوپ یک عنصر ناپایدار بوده که به واسطه یک نوترون یا پروتون اضافه نسبت به ایزوتوپ های دیگر خود ناپایدار می باشد و برای رسیدن به پایداری از خود اشعه گاما ساطع می نماید. درنتیجه رادیوایزوتوپ ها برای پرتودهی نیاز به انرژی الکتریکی ندارند. Co60 و Ir192 نمونه هایی از رادیوایزوتوپ های ناپایدار هستند. هرچقدر فرکانس اشعه ایکس یا گاما بالاتر باشد دارای انرژی بیشتری بوده که اگر با مدت زمان مناسبی استفاده شود موجب افزایش دانسیته تصویر رادیوگرافی شده اما تضاد تصویر را کاهش می دهد. انرژی یک هسته ناپایدار یا قدرت تخریب آن توسط پارامتری به نام کوری بیان می شود.
کوری آهنگ واپاشی هسته های ناپایدار در یک گرم از عنصر رادیوم به ازای واحد زمان می باشد.
یکی از فاکتورهای مهم در تشخیص کیفیت رادیوگرافی حساسیت تصویر ایجاد شده می باشد. حساسیت تصویر تشکیل شده به صورت کوچکترین عیب مصنوعی قابل روءیت به ضخامت قطعه می باشد. منظور از عیب قابل تشخیص، شاخص کیفیت تصویر (IQI) می باشد که به صورت عامدانه در حین رادیوگرافی استفاده می شود. هر بسته IQI دارای یک بسته سیم با قطرهای مختلف در کنار یکدیگر است که هرچقدر سیم هایی با قطر کوچکتر در تصویر قابل تشخیص باشد آن تصویر حساسیت بالاتری دارد. بسته IQI باید در جایی قرار گیرد که سختگیرانه ترین حالت رعایت شود. جنس IQI باید همجنس قطعه باشد. در غیر اینصورت جنس IQI باید ضعیف تر از جنس قطعه باشد. اگر جنس IQI قوی تر از فلز جوش باشد تصویر واضح تری از خود ایجاد کرده درنتیجه سختگیرانه ترین حالت ایجاد نمی شود. بسته IQI باید روی فلز جوش و عمود بر خط جوش قرار گیرد.
زمان پرتودهی یکی از مهم¬ترین پارامترهای عملیات رادیوگرافی می باشد. اگر زمان پرتودهی کم باشد دانسیته تصویر ایجاد شده کم بوده که منجر به تضاد تصویر پایین می-شود. اگر زمان پرتودهی بیش از حد لازم باشد دانسیته تصویر بیش از حد افزایش یافته و تصویر فلز جوش از دیگر نقاط فیلم قابل تشخیص نیست. درنتیجه به ازای قدرت چشمه رادیواکتیو یا دستگاه اشعه ایکس مورد استفاده، فاکتور فیلم خام، فاصله منبع اشعه تا فیلم و ضخامت فلز جوش مورد بررسی یک مدت زمان بهینه ای وجود دارد که از طریق روابط موجود در منابع قابل تعیین است.
-
رادیوگرافی
رادیوگرافی
-
خطوط انتقال گاز
خطوط انتقال گاز
-
مواد تغییر فاز دهنده و بازده انرژی ساختمان ها
مواد تغییر فاز دهنده و بازده انرژی ساختمان ها